Der folgende Artikel ist nicht auf meinem Mist gewachsen. Ich stelle lediglich die Inhalte des Einstellfahrplans von 3DDC hier für Interessierte zur Verfügung, da die Site 3DDC nicht mehr erreichbar ist und ich in diversen Foren fragen zum Einstellfahrplan gelesen habe.
Die Inhalte sind 1:1 kopiert, wobei ich die Einleitung und einige „Unterstützungshilfen“ weggelassen habe. Vielen Leuten geht es um die Slicereinstellungen, damit die Floweinstellungen eingestellt werden können.
Urheber ist das 3DDC Team. Nach bestem Wissen und Gewissen namentlich: Evolution, c1olli und paranoid.
Sollte ich Personen nicht genannt haben, so ist das nicht als Affront zu werten, sondern Unwissenheit.
Ich hoffe somit der Creativ Common Lizenz ausreichend nachgekommen zusein, damit wir auch einsteigen können.
Voraussetzungen / Erwartungen
- Ihr solltet euch bereits mit eurem Drucker und der Software eingehend beschäftigt haben und beides sicher bedienen können. Gewöhnt Euch an die englischen Ausdrücke zu nutzen, denn die deutschen Ausdrücke führen gerne mal zu Verwirrungen. Wir werden hier keinem erklären wie der Drucker/Software bedient werden muss.
- Den Drucker per Gcode über ein Terminal bedienen zu können, kann nicht schaden ist aber auch kein Muss, da viele Funktionen auch über das Display des Druckers abgearbeitet werden können, aber dies ist je nach Modell verschieden. Programme dafür sind Pronterface, Octoprint und Repetier Host.
- Die Einstellungen/Arbeitsschritte genau so wie beschrieben machen, auch wenn ihr es aus anderen Quellen (Youtube/Facebook) anders gewohnt seid, denn Ihr erarbeitet hier ein auf den Drucker zugeschnittenes Profil.
- Ihr müsst euch bewusst machen, dass es im 3D-Druck keine Abkürzungen gibt.
Hinweis: Arbeitet den Fahrplan gewissenhaft durch, lest den Thread sowie die verlinkten Beiträge erst einmal komplett durch, bevor Ihr mit dem Drucken beginnt, denn viele Fragen erklären sich dann selbst.
1. Vorbereitungen
Eine gute Vorbereitung erspart einem später den einen oder anderen Umweg. Also geht akribisch an die Sache, um so leichter wird es zum Ende heraus sein.
Hinweis: 3DDC hat mit zwei Filamenthersteller einen Einstellfahrplan-Filament in Staubgrau entwickelt, indem die Fehler wohl einfach zu sehen sind. Die beiden Hersteller sind: Material4Print und BavariaFilament.
1.1 Drucker Aufbau kontrollieren
Baut Euren Drucker gewissenhaft auf, jede Schludrigkeit sieht man später im Druck.
Bitte prüft euren Drucker:
– auf Rechtwinkligkeit
– auf ordentliche Verschraubung
– auf leichtgängige Achsen (insbesondere Z)
– auf korrekte Riemenspannung
– auf ein korrekt montiertes Hotend (ggfs. neu zusammenbauen)
– sorgt für ordentliche Kühlung (ggfs. Lüfter ersetzen)
– Sorge für ein gut geleveltes Bett siehe auch Bettabstand und Brim
– Schaut auch auch an, ob der Feeder brauchbar ist
– Die Steps der X, Y, Z Achse sollen auf den Werkseinstellungen, bzw. den aus der Hardware vorgegebenen Steps (z.B. X80, Y80, Z400) stehen. Keinesfalls die Steps nach der Größe von Druckteilen einstellen!!!
1.2 Extrusion kalibrieren
Warum muß der Feeder (Extruder) kalibriert werden?
Damit wir eine einheitliche, nachvollziehbare Grundlage haben und der Feeder (Extruder) auch tatsächlich die gewünschte Menge fördert, denn je nach Feeder ist das unterschiedlich.
Die Grundeinstellung vom Werk aus passt in den allerwenigsten Fällen.
Viele Drucker kommen auch mit sehr schlechten Feedern, daher ist es ratsam sich gleich nach anständigen Alternativen umzuschauen. Siehe dazu auch Welcher Extruder/Feeder soll es sein?
Hier ist eine tolle Anleitung, um die Extrusion zu kalibrieren.
1.3 PID Tuning
In den Firmwares unserer Drucker gibt es das sogenannte PID Regelung. Dies ist eine Art Regelautomatik, um die Temperaturen von Hotend und Bett möglichst stabil zu halten.
Im Unterschied dazu gibt es den „Bang – Bang“ Mode (meistens Heatbed), wo dann die Heizung nur ein und aus geschaltet wird, was zu starken Stromschwankungen führt, die sich dann im Druckbild widerspiegeln.
Falsche Einstellungen können sich sogar im Druck zeigen. Deswegen besser gleich PID Tuning durchführen.
2. Die Praxis
2.1 Slicer Profil erstellen
Erstelle ein neues Slicer Profil mit folgenden Angaben:
Neues Grundprofil (Default / Werkseinstellungen) – nichts voreingestelltes (auch kein vorgefertigtes)
Parameter Cura:
Line Width (LW) | 0,40 (LW ≙ Düsendurchmesser) |
Flow | PLA = 90%, PETG = 95%, ABS/ASA /PC,/POM,/HIPS,/TPU= 100% |
Printing Temperature | Ermittelt durch Heattower |
Layer Height (LH) | 0,1mm (ggf.Initial Layer Height 0,2mm) |
Print Speed | 60mm/s (oder auch mehr, wenn das Gerät es kann. z.B: Ratrig/Voron) |
Wall Speed | 30mm/s |
Initial Layer Speed | 20mm/s |
Top/Bottom Speed | 30mm/s |
Wall Thickness | 0 |
Wall Line Count | 2 |
Top Layers | 10 |
Bottom Layers | 10 |
Infill Density | 15% |
Infill Pattern | Grid |
Retraction Distance | Direct Drive Extruder = 1,0 +/- 0,5mm, Bowden Extruder = 3mm Grundeinstellung. Oder für Profis – Bowdenspiel + 1,0 +/- 0,5mm Der Wert wird im Verlauf der Einstellungen noch genauer justiert. |
Fan Speed | 100%(Automatik, bei ABS ggf. aus) |
Diameter | Ermittelter Filamentdurchmesser |
Wichtig! | |
Alternate Extra Wall | DEAKTIVIERT |
Extra Skin Wall Count | 0 |
Extra Infill Wall Count | 0 |
Horizontal Expansion | 0 |
Outer Wall Wipe Distance | 0 |
Enable Ironing | DEAKTIVIERT |
Enable Coasting | DEAKTIVIERT |
Combing | Off |
Retraction Extra Prime Amount | 0 |
Parameter PrusaSlicer:
Default Extrusion Width (EW) | 0,40 (LW ≙ Düsendurchmesser) |
First Layer (EW) | 0,4 |
Perimeters, External Perimeters (EW) | 0 |
Infill, Solid Infill, Top Solid Infill (EW) | 0 |
Elephant foot compensation | 0 |
Extrusion multiplier (EM) | PLA = 90%, PETG = 95%, ABS/ASA /PC,/POM,/HIPS,/TPU= 100% |
Temperature Extruder | Ermittelt durch Heattower |
Layer Height (LH) | 0,1 mm (ggfs. First Layer Height 0,2mm) |
Speed for print moves Infill | 60 mm/s |
External perimeters Top Solid Infill Solid Infill Small perimeters | 30mm/s |
First layer speed | 20 mm/s |
Perimeters | 2 |
Solid layers top | 10 |
Solid layers bottom | 10 |
Fill Density | 15% |
Fill Pattern | Rectilinear /Grid |
Retraction Length | Direct Drive Extruder = 1,0 +/- 0,5mm, Bowden Extruder = 3mm Grundeinstellung. Oder für Profis – Bowdenspiel + 1,0 +/- 0,5mm Der Wert wird im Verlauf der Einstellungen noch genauer justiert. |
Retraction Speed | 25-50 mm/s |
MAX Fan Speed | 100%(Automatik, bei ABS ggf. aus) |
MIN Fan Speed | 0-50% |
Machine Limits | Ignore |
Diameter | Ermittelter Filamentdurchmesser |
Wichtig! | |
Detect thin walls | DEAKTIVIERT |
Extra Perimeters if needed | DEAKTIVIERT |
Extra length on restart | DEAKTIVIERT |
Wipe while retracting | DEAKTIVIERT |
X Y Size Compensation | DEAKTIVIERT |
Parameter Simplify 3D
Extrusion Width (EW) | 0,40 (EW ≙ Düsendurchmesser) |
Extrusion Multiplier (EM) | PLA = 90%, PETG = 95%, ABS/ASA /PC,/POM,/HIPS,/TPU= 100% |
Primary Extruder Temperature | Ermittelt durch Heattower |
Primary Layer Height (LH) | 0,1mm (ggf. First Layer Height 0,2mm) |
Default Printing Speed | 60mm/s |
Outline Underspeed | 50% = 30mm/s |
First Layer Speed | 33% = 20mm/s |
Solid Infill Underspeed | 50% = 30mm/s |
Outline/Perimeter Shells | 2 |
Top Solid Layers | 10 |
Bottom Solid Layers | 10 |
Interior Fill Percentage | 15% |
Internal Fill Pattern | Rectilinear/Grid |
Retraction Distance | Direct Drive Extruder = 1,0 +/- 0,5mm, Bowden Extruder = 3mm Grundeinstellung. Oder für Profis – Bowdenspiel + 1,0 +/- 0,5mm Der Wert wird im Verlauf der Einstellungen noch genauer justiert. |
Retraction Speed | 25-50mm/s |
Fan Speed | 100%(Automatik) |
Diameter | Ermittelter Filamentdurchmesser Vermesst neue Rollen mit einem Messschieber (Messuhr) über 10m pro Messort 3x in verschiedenen Winkeln (alle 60°), bildet den Durchschnitt und notiert den FD (Filamentdurchmesser) gleich auf der Spule. |
Wichtig! | |
Coast at End | DEAKTIVIERT |
Wipe Nozzle | DEAKTIVIERT |
Horizontal Size Compensation | DEAKTIVIERT |
Bei Sägezahn ähnlichen Wänden | Einstellung unten testen |
Start Points | Choose start point closest to specific position X, Y 100 |
Alle nicht explizit angesprochenen Einstellungen bleiben beim Default Wert, werden also nicht geändert.
In der Firmware Linear Advance deaktivieren. (M900 K0 im Start Gcode schaltet lin_advance aus)
Dieses Profil mit den Grundeinstellungen ist die Grundlage für die folgenden Schritte.
2.2 Heattower drucken
Drucke den mittleren (medium) Heattower aus dem Forum von 3DDC.
Siehe Erstellung eines Heattowers
- „Minimum Layer Time“ (Cura)/ „Slow down if layer print time is below“(Prusa Slicer) auf 0
- EW/LW = Düsendurchmesser, EM/Flow = PLA 0,9/90% (PETG 95%, ABS 100% entsprechend)
- Kühlung = Aus (je nach Material auch mit Kühlung, am besten beides)
- Temperatur – gute Bereiche für die einzelnen Materialien sind:
- PLA: 230 – 185
- PETG: 250 – 205
- ABS/ASA: 260 – 215
- Vase Mode einschalten!
- Drucke mit der Geschwindigkeit, die hier vorgegeben wird, denn die sollte von jedem Drucker fehlerfrei gedruckt werden. Später, wenn man sein Gerät kennt, kann man dann immer noch schneller drucken.
- Mach die Fingernagelprobe – teste bei welcher Temperatur die Layer am besten haften.
Tipps zur Beurteilung:
Der Heattower zeigt mir zuerst einmal die Temperatur an, bei der sich das Filament wohl fühlt. Hierzu schaue ich mir an wo bezogen auf die Kanten, den Glanz und die Ablage und die Haltbarkeit (Fingernagelprobe in der Mitte der Temperaturbereiche) das Optimum erreicht wird.
Für PLA liegt das bei unseren Geschwindigkeiten so zwischen 190 und 215°C. (M4P ca. 210-215°C, Bavaria 205-210°C)
Aber der Heattower hat noch mehr zu bieten z,B.
– gequetschte Layer weisen auf eine klemmende Z-Achse hin
– Extrusionsaussetzer
– Rattermarken durch defekte Lager etc.
– Am Anfang einer Bahn Macken durch zu hohen Jerk
– Betthaftung
3. Die Einstellprozedur
Warum diese Prozedur ? Was passiert da?
Die verschiedenen Slicer Profile, bzw. empfohlene Einstellungen sind pauschal und gehen nicht auf die Gegebenheiten des einzelnen Druckers ein. Fast immer aber wird viel zu viel Material gefördert, was ein unschönes Druckbild zur Folge hat.
Man kann sich das Extrusionssystem wie einen Spritzbeutel zum Dekorieren von Torten vorstellen. Um hier ein anständiges Ergebnis zu bekommen, muss man auch mit Gefühl fein dosiert vorgehen. Einfach draufdrücken endet in einem riesigen Klecks.
Genau das aber passiert bei einer Linienbreite von 0,4 (bei 0,4mm Nozzle) und 100% Flow. Der Extruder schiebt das Filament in das Hotend und erzeugt einen Überdruck, der sich dann in dicken Linien, Klecksen, Blobs etc. entlädt. Besonders gut sieht man das wenn nach Extrusionsende immer noch fröhlich Material aus der Düse kommt, weil der innere Überdruck jetzt abgebaut werden kann. (Bei der richtigen Einstellung von EW / EM / Temp. wird auch das Nachlaufen via Schwerkraft gehemmt, kann aber nicht zu 100% ausgeschlossen werden).
Mit der obigen Methode werden 2 Ziele verfolgt: Feineres Druckbild durch feinere Linien und Abbau des Überdrucks durch Reduzierung des Flows. Toller Nebeneffekt ist, dass sich in der Regel die Maßhaltigkeit verbessert.
Durch die Reduzierung der Linienbreite werden mehr Linien pro Abschnitt gedruckt und auch schon ein wenig der Flow reduziert. Anschlüsse an Wände haben weniger Lücken (je nach LW).
Die Reduzierung des Flows nimmt dem System den Überdruck was dann auch zur gewünschten Außenform führt. Ecken sind Eckig, Flächen glatt ohne Blobs und beim Retract läuft kein Material mehr nach.
Gleichzeitig wird die Temperatur im Hotend stabiler, da die Heizpatrone weniger Material pro Zeiteinheit heizen muß. Da der Thermistor nicht direkt in der Schmelze hängt, bekommt man das nicht mit.
Da sich die Anzahl der Linien erhöht dauert der Druck etwas länger, kann aber durch höhere Druckgeschwindigkeit, vorausgesetzt die Mechanik macht das mit, kompensiert werden. Dabei natürlich die Temperaturen, wenn nötig, anpassen.
Auf der Suche nach der besten Einstellung werden eine Menge Würfel gedruckt werden müssen, also nicht verzweifeln, das gehört dazu. Auch muß man nicht alles auf einmal machen, oft ist es besser sich Zeit zu lassen und das Ganze sacken zu lassen.
3.1 Würfel mit Loch
Drucke den Würfel mit Loch Version 2 mit folgenden Einstellungen: (Gültig für 0,4mm Düse)
– LW / EW = 0,48 (Düsendurchmesser (ND) +20%)
– Min_Layertime wieder auf Standard
– alle anderen Einstellungen wie im Profil
!!Retract bleibt natürlich an (Basisfunktion)!!
Drucke noch einen Würfel mit Loch (es werden noch viel mehr, aber das ist nicht zu vermeiden):
– LW / EW = 0,40 (ND)
der Rest der Einstellungen bleibt identisch.
Für größere Düsendurchmesser gibt es bei den Druckteilen eine größere Version.
Diese beiden Würfel sind unsere Referenz. Wenn man diese später mit dem Endergebnis vergleicht, dann weiß man was das Einstellen gebracht hat. Der Würfel ist 20 x 20 x 10mm groß (ohne Nubsi)
Diese Einstellungen sind ab hier fix und werden nur in Punkto LW/EW bzw. Flow/EM geändert. Und dabei immer nur eine einzige Änderung. Dies ist wichtig, da man sonst der Prozedur nicht mehr folgen kann, weil man bei mehreren Einstellungen gleichzeitig nicht weiß welche Einstellung welche Auswirkung hatte.
Dazu gehören auch das Wechseln des Slicers, Umbauten am Hotend, wechseln des Filaments, Änderung von Einstellungen im Slicer oder der Firmware usw. Aktionismus führt zu nichts und im Zweifel muss mit der Einstellprozedur von vorne begonnen werden.
Wenn ihr z.B. Änderungen im Slicer testen wollt, macht euch eine Kopie des Profils und testet damit. So kann man jederzeit am vorherigen Stand weiter arbeiten. Veränderungen an der Hardware des Druckers sollten dennoch weiterhin unterlassen werden. Achtet darauf, nicht mehrere Parameter auf einmal zu ändern.
Immer einen Schritt nach dem anderen.
Ja diese Prozedur ist aufwändig und kostet viel Zeit, aber das lässt sich nicht vermeiden. Und die Helfer investieren genauso viel Zeit hier, um Dir das Wissen zu vermitteln.
Beachte eine Gesetzmäßigkeit des Druckes:
Kälter = niedrige , breite Perimeter/Layer**
Heißer = höhere , schmale Perimeter/Layer**
Jede Änderung eines Wertes zieht Änderungen anderer Faktoren nach sich – erhöhe ich die Geschwindigkeit, sinkt die Temperatur im Hotend – Layer wird breiter.
Jetzt werden dann LW / EW sowie später dann der Fluss / EM nach und nach immer weiter nach unten justiert, denn der Drucker kann viel feiner als der Düsendurchmesser drucken > mehr Linien > feinere Auflösung . Vor allem wird auch der Flow runtergeregelt, denn die meisten drucken mit viel zuviel Material gerade bei PLA. Bei PETG und ABS muß der Flow aufgrund der Schrumpfung höher sein.
Weil ich das anfangs auch nicht wusste habe ich mich gewundert, warum die Oberflächen in ABS so klasse waren, in PLA aber nicht => Grund waren die, bis auf die Temperatur, identischen Einstellungen.
Was passiert im Detail?
Erst EW/LW in 0,01er Schritten also 0,39 , 0,38 …bis 0,30 (max.) verringern, bis die Oberfläche sauber geschlossen ist. Bei anderen Düsendurchmessern – ND-25%
Schließt sich der Würfel bis LW 0,30 nicht, kann fehlendes Material ein Grund sein, das kann verschiedene Ursachen haben, wie falsche Kalibrierung, fehlende Extruderschritte, Hotend falsch zusammengebaut, schlechte Komponenten etc.
Ist der Würfel schon z.B. LW 0,40 geschlossen, ist der Flow wahrscheinlich viel zu hoch. Trotzdem den LW bis 0,30 reduzieren und dann den Würfel mit der gleichmäßigsten Oberfläche wählen (meist zwischen LW 0,35 und 0,30). Es zählt ab 3mm vom Rand aus für die Bewertung offen/geschlossen (und natürlich die Perimeter untereinander selbst). Der Umlenkungsbereich zählt quasi nicht.
Den entsprechenden Würfel herausnehmen und bei dem Wert Bsp. EW/LW=0,33 dann langsam (0,01er/1% Schritte) den EM/Flow verringern (0,89/89% , 0,88/88%…max. 0,8/80%) bis die Bahnen beginnen aufzubrechen. Dies entfernt das noch überschüssige Material.
Der Würfel der noch geschlossen ist, ist wieder die Referenz. Am Ende passt man noch den „Initial Layer Flow“ an, damit Seite der Würfel auch schön gerade wird (kein Elefantenfuß).
Also nicht wundern, wenn der Würfel mit einer Linienbreite von 0,3mm und einem Fluß von 82% (EM=82) gedruckt werden muss – einfach machen.
Bei dem Prozedere können auch noch Fehler im System festgestellt werden, die dann durch entsprechende Drucke verifiziert werden, das ist ganz normal.
Beachte auch die Höhe der Bauteile – der Würfel ist ohne Nubsi genau 10mm hoch. Wenn die Höhe nicht passt, dann entsprechend leveln. Sollte das nicht funktionieren, weil der Würfel nicht mehr haftet und er wird nicht hoch genug, so liegt das sehr oft an einer klemmenden Z-Achse.
Tipps zur Beurteilung
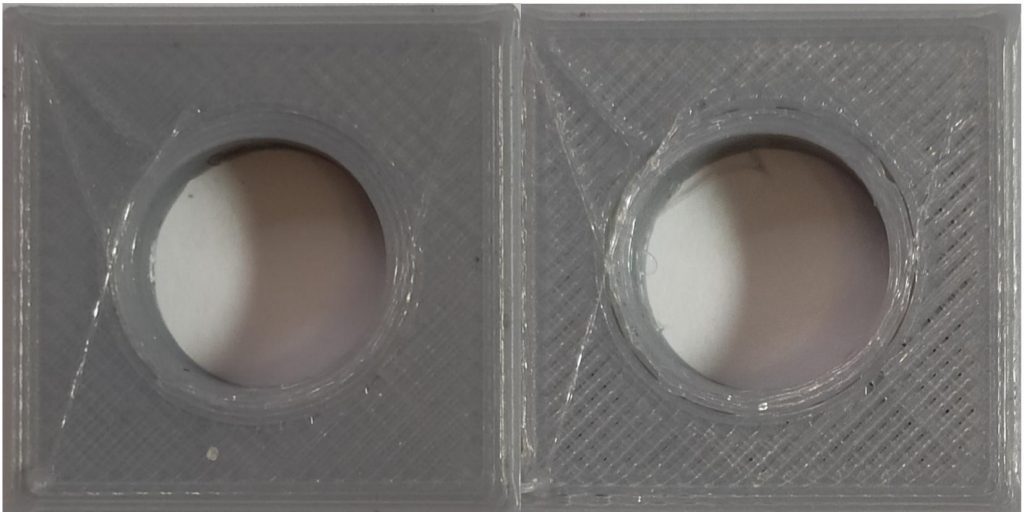
Links geschlossen, Rechts offen.
Im rechten Bild sieht man durch die Lücken den 2. Layer das nennen wir offene Bahnen. Im linken Bild sind keine Zwischenräume, durch die man die darunter liegenden Layer sehen könnte – die Oberfläche/Bahnen sind geschlossen. Geschlossen ist, wenn man die Bahnen drunter nicht erkennen kann, also wenn alle Bahnen durchgehend miteinander verbunden sind. Meistens findet sich der Sweetspot dann zwischen 0,35 und 0,30. Dies ist dann der Würfel mit der schönsten Verteilung bei geschlossener Oberfläche.
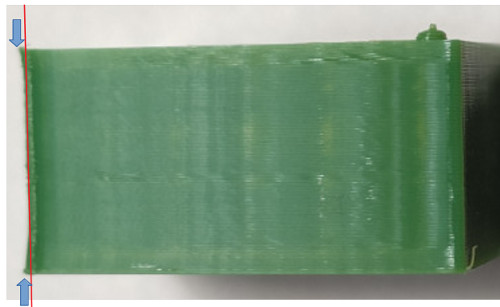
An der Seitenansicht des Würfels erkennt man unten den sogenannten Elefantenfuß und oben einen Kragen. Wenn die Höhe das Würfels stimmt, heißt dass, das der First Layer Flow zu hoch ist und der Gesamtflow auch. Da sich die ersten und letzten 10 Schichten nicht nach innen ausbreiten können, diese werden ja voll gedruckt, bleibt nur der Weg nach außen. Hier muß also erst der Gesamtflow reduziert werden und dann ggf. noch der First Layer Flow, bis der Würfel eine gerade Seite hat.
3.2 50×50 Quader
Mit dem nun aus den Würfeln erarbeiteten Voreinstellungen drucken wir den Quader 50 x 50 x 5. Hier wird geschaut ob mit dem Setup auch längere Bahnen funktionieren. Ggf. werden die Einstellungen noch angepasst / verfeinert. Gerade Objekte mit langen Bahnen benötigen eine stabile Temperatur im Hotend.
Die Bewertung des Quaders ist in vielen Punkten gleich der Bewertung des Würfels, aber hier wird genau auf die Ablage der Bahnen geachtet, da hier aufgrund der Länge der Bahnen auch das Hotend mehr gefordert ist. Es kann durchaus sein, dass die Basistemperatur nicht ausreicht und daher nicht genügend Material geschmolzen wird und Aussetzer die Folge sind. Am Quader tritt der Kragen der Deckschicht bei zu viel Flow noch stärker hervor, kann aber oft nicht ganz vermieden werden.
3.3 Pyramide
Die Pyramide vereint verschiedene Komponenten. Unten eine relativ große Fläche, dann dünne Beine und oben die Spitze. Hier wird die Prozeßstabilität für alle Bereiche optimiert, gerade an den Beinchen bilden sich gerne Stringing und Ablagerungen, die durch die perfekte Einstellung von LW / Flow / Temperatur sowie des Retracts vermieden werden können. Bildet sich auf der Spitze ein Hut, ist der Flow noch zu hoch.
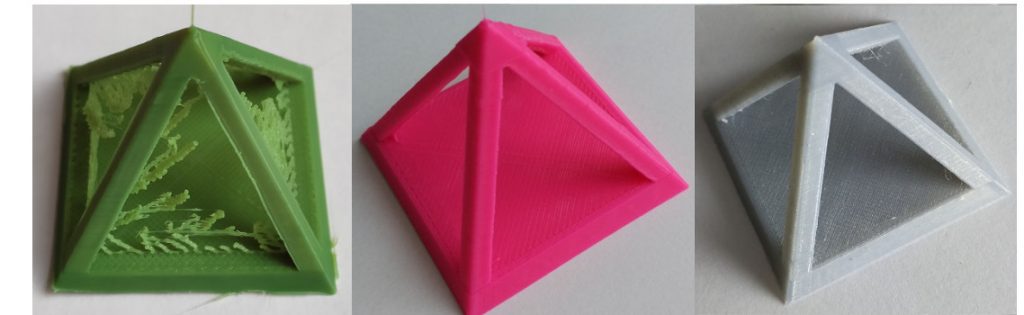
Links: Material aus der Düse läuft nach
Mitte: Hütchen
Rechts: gut
Im linken Bild läuft Material aus der Düse nach. Das kann folgende Gründe haben:
– Zuviel Material
– Zu hohe Temperatur
– Eine Kombination aus beidem
Das kommt daher, dass bei der Fläche ganz andere Voraussetzungen herrschen als bei den Beinchen – perfekt wäre hier ein geteilter Druckablauf, der z.B. bei den Beinchen eine etwas niedrigere Temperatur hat.
Bei der mittleren Pyramide ist dort wo die Beinchen zusammenlaufen ein Absatz (das sogenannte Hütchen), das ist ein Indiz für einen etwas zu hoch eingestellten Flow. Oft lohnt sich hier ein Vergleichsdruck mit einem höherem LH (z.B 0,2)
Heattower Evolution
Der Heattower Evolution ist ein neues Mittel, um Fehler im Drucksystem zu finden und noch genauer analysieren zu können.
Bescheibung ist in Arbeit